Why it is important to conduct risk assessment at workplace?
Before the Risk Assessment (Preparation):
Understanding the Scope:
1.Identifying the Area/Activity: Clearly defining what specific area, task, or process will be assessed. This could be a specific work area (like a loading dock), a particular activity (like using a forklift), or a process (like chemical mixing).
Legal and Regulatory Requirements: Knowing the relevant health and safety legislation, industry standards, and company policies that apply to the assessed area/activity. This ensures compliance.
Gathering Information: Reviewing existing safety data, previous incident reports, equipment manuals, process documentation, and any other relevant information.
Assembling the Team (If Necessary): Depending on the complexity of the assessment, the safety officer might involve other stakeholders, such as:
2. Employees who perform the tasks: They have valuable firsthand knowledge of potential hazards.
Supervisors and managers: They can provide insights into procedures and resource allocation.
Technical experts: They might be needed for assessing specific equipment or processes.
3. Choosing the Methodology: There are different risk assessment methodologies (e.g., HAZOP, JHA, 5×5 Risk Matrix). The safety officer will choose a method appropriate for the situation.
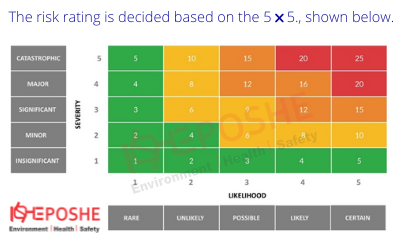
When conducting Risk Assessment
1. Hazard Identification:
Systematically looking for potential sources of harm: This involves examining every step of the process or every aspect of the area being assessed.
Considering a broad range of hazards:
-
- Physical hazards: e.g., slips, trips, falls, machinery, noise, radiation.
-
- Chemical hazards: e.g., toxic substances, corrosives, flammable materials.
-
- Biological hazards: e.g., bacteria, viruses, fungi.
-
- Ergonomic hazards: e.g., poor posture, repetitive movements, heavy lifting.
-
- Psychological hazards: e.g., stress, bullying, harassment
Using various techniques to identify hazards:
-
- Walk-through inspections: Observing the workplace firsthand.
-
- Talk to workers: Gathering information from those who perform the tasks.
-
- Reviewing past incidents and near misses.
-
- Consulting relevant literature and databases.
2. Risk Analysis:
Evaluating the likelihood of each hazard causing harm: How often does exposure to the hazard occur, or how probable is it that an incident might happen?
Evaluating the severity of the potential harm: What could be the potential consequences of an incident (e.g., minor injury, serious injury, fatality)?
Using a risk matrix or scoring system: This is often done to objectively prioritize risks. The matrix usually combines likelihood and severity to determine the overall risk level (e.g., low, medium, high).
Considering who might be harmed: Employees, contractors, visitors, members of the public?
3.Risk Evaluation
Comparing the analyzed risk levels against pre-defined risk tolerance criteria: Is the level of risk acceptable, or does it require further action?
Determining whether existing control measures are adequate: Are current procedures and equipment effectively controlling the identified risks?
4.Risk Controls – Developing Control Measures
Following a hierarchy of control (most effective to least effective):
-
- Elimination: Remove the hazard entirely.
-
- Substitution: Replace the hazardous substance or process with a less hazardous one.
-
- Engineering controls: Implement physical changes to the workplace or equipment (e.g., guards on machinery, ventilation systems).
-
- Administrative controls: Change work procedures or policies (e.g., safe work procedures, job rotation).
-
- Personal Protective Equipment (PPE): Provide workers with PPE (e.g., gloves, safety glasses). PPE should always be a last resort.
After the Risk Assessment (Implementation and Review):
Documenting the Risk Assessment:
-
- Clearly recording all findings: Identified hazards, analyzed risks, evaluated risk levels, and recommended control measures.
-
- Using clear and concise language: The document should be easily understood by all relevant parties.
-
- Keeping the document readily available: Ensuring the information is accessible for workers and supervisors.
Communicating the Findings:
-
- Sharing the risk assessment results with relevant stakeholders: Informing workers, supervisors, and managers about the identified risks and control measures.
-
- Providing training on new control measures: Ensuring workers understand how to work safely with new procedures and equipment.
Implementing the Control Measures:
-
- Ensuring the control measures are put in place as recommended.
-
- Monitoring the effectiveness of the implemented controls: Are the control measures working effectively to reduce risks?
Regular Review and Updates:
-
- Periodically reviewing the risk assessment: The frequency of review depends on the level of risk and the nature of the activities. This is especially important after any significant changes in the workplace, procedures, or equipment.
-
- Revising the risk assessment as needed: Adjusting the assessment to address new hazards or changes in risk levels.
Key Qualities of a Safety Officer Performing a Risk Assessment:
-
- Knowledgeable: Possesses a strong understanding of health and safety legislation, best practices, and relevant industry standards.
-
- Analytical: Able to critically evaluate hazards, assess risks, and develop appropriate control measures.
-
- Observant: Pays close attention to details and can identify potential hazards that might be overlooked.
-
- Communicative: Can effectively communicate risk assessment findings and recommendations to diverse audiences.
-
- Proactive: Takes initiative to identify and address safety concerns.
-
- Organized: Keeps accurate records and documents the assessment process effectively.
Summary
In summary, a safety officer performing a risk assessment is a systematic process of identifying hazards, analyzing risks, evaluating their severity, and implementing appropriate controls to minimize the likelihood of accidents and injuries. It’s a crucial function in creating a safe and healthy workplace.